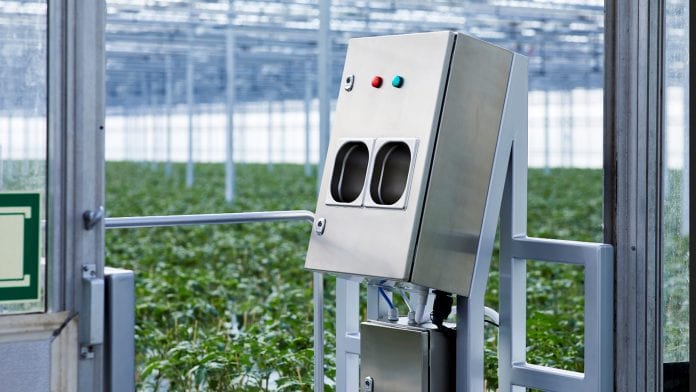
Steriloc is a cost effective, efficient, robust, and environmentally friendly automatic hand sanitisation system which enables staff, customers, visitors or students to ensure they have safely disinfected their hands.
Steriloc is an antivirus entry system which, when connected to an access setup, allows people to enter a workplace, school, community hub or gathering place only if their hands are quickly and thoroughly cleansed with a powerful automatic touch free hand sanitiser. Once a person has cleansed their hands, an electrical signal triggers a door catch or turnstile, ensuring that your workplace hygiene is not compromised.
What are the benefits of Steriloc?
Steriloc will demonstrate your commitment to achieving a COVID-19-free workplace; and will form a key part of your risk mitigation strategy, offering reassurance to the workforce that their return to work is as safe as can be during the pandemic. Manufactured in the UK to exceptional standards, it is surprisingly affordable for something that can reduce sick days, give customers added confidence and protect your employees, visitors, students and patients.
Everyone is now acutely aware of how easily and quickly viruses can spread. They can affect everything from the health of your workforce and customers to product contamination. Steriloc instantly cuts the risk of cross-contamination – and has been proven to reduce absenteeism in the workplace.
The Steriloc system is:
- Effective (no cleansing, no entry)
- Economical
- Efficient (processes up to 30 people a minute)
- Safe
A system developed in partnership with Extreme Low Energy Ltd (ELe) uses low voltage energy to allow operation away from a power supply and reduces installation costs.
Steriloc units can be attached to free-standing units, desk-mounted or wall mounted. They can be easily linked to entry mechanisms; and can be used with an extensive range of sanitising liquids available in our marketplace.
How does coronavirus spread in the workplace?
While there has been much focus in the media on businesses deciding to continue with home working for many of their employees, the fact remains that the majority of us either have already returned or will soon return to a workplace of some kind. Whether it is an office, factory, warehouse, shop or hospitality venue, there will likely be a large number of communal spaces and face-to-face interactions involving shared objects and surfaces.
According to the World Health Organization (WHO), when someone who is infected with COVID-19 coughs or exhales they expel droplets containing the virus, most of which fall onto nearby surfaces and objects. Put this into a workplace context and research tells us that shared objects and surfaces including doors, drawer handles and kitchen equipment such as refrigerators, taps and coffee pots have the highest concentration of germs. This means that the more employees touch shared surfaces, the higher the risk of contamination and infection.
Another more detailed study by the American Society for Microbiology looked at the rate at which viruses can spread through the workplace. By placing a sample of a harmless virus on a single doorknob or tabletop in an office building, researchers found that the first area to be contaminated was the coffee break room. Within two to four hours, the virus could be detected on 40% to 60% of workers, visitors, and commonly touched objects.
For a virus to become harmful, it must be brought into the body. Until the COVID-19 pandemic, few of us understood just how easily this can happen. We now know that we typically touch our faces around 25 times an hour and that it is areas such as our nose, eyes, and mouth where viruses most frequently enter the body.
Where does hand sanitisation fit in?
Given these facts, we can now appreciate more than ever the need to prioritise hand sanitisation to reduce the risk of contamination, particularly in the workplace. While it may not be practical or realistic to expect employees to wear face coverings in many work situations, ensuring thorough hand cleansing and regular cleaning of frequent touchpoints will considerably reduce the spread of viruses. Furthermore, by locating permanent touch-free hand sanitisation stations at workplace entry points, viruses can be prevented from entering a building via hands in the first place.
Steriloc touch-free hand sanitisers are robust units that are designed to be easily integrated with building access systems. No sanitisation means no entry.
Five things to consider when installing an effective hand sanitisation station
-
How robust is your dispenser?
Whatever mechanism you use to dispense sanitiser, it is important that it is strong enough to withstand the volume of doses it will need to make – this can often be underestimated.
-
Is your system touch-free?
Multiple numbers of potentially infected fingers placed on a pump dispenser one after the other makes having a hand sanitiser ultimately less effective. Touch-free systems will significantly cut down the risk of infection; and should be the only method used.
-
How best to manage sanitiser storage and replenishment
It is important to ensure that your units include a secure space for the sanitiser liquid. The Steriloc system includes a separate lockable area to house the sanitiser. A connected, automated sanitisation system which notifies those responsible when liquid levels are low is the most effective way to ensure a seamless, continuous supply of sanitiser.
-
Can users choose whether to sanitise or not?
Mandatory sanitising units integrated to building entry systems, where access is denied if hands are not sanitised, are by far the best way to ensure that every entrant has effectively cleansed hands.
-
What else can your Steriloc system do for you?
Working with our systems partners at Circular 1 Health, we have ensured Steriloc units can now measure and record a person’s temperature, time of entry and exit whilst confirming sanitisation. The Steriloc system has the capability to link with your track and trace protocols.
Nick Denham
Director
Steriloc
sales@steriloc.com
www.linkedin.com/company/steriloc
Steriloc.com
This article is from issue 15 of Health Europa. Click here to get your free subscription today.